500kg 1ton load warehouse logistics agv robot uses two-dimensional code inertial navigation operation, high precision and fast speed; with automatic avoidance obstacles, posture retention and other powerful functions to transport the shelves where the goods are located from the huge warehouse storage area to the staff processing area, greatly improving Processing efficiency.
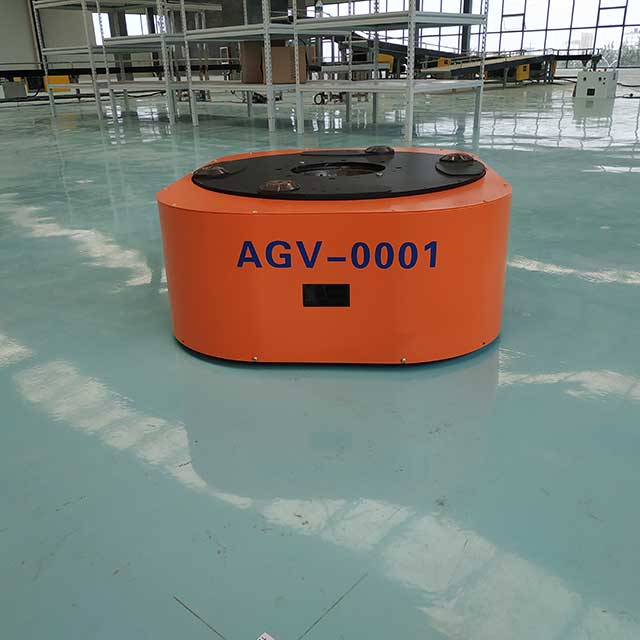
The operating principle of Logistics agv:
After receiving the instruction from the work center, the AGV guides it to the cargo loading position by the navigation system. After the loading is completed, according to the preset instruction, after analyzing the starting point-end point path, the optimal walking path is planned and walked to the designated position. In the process, the two-dimensional code navigation system is continuously used to identify the surrounding feature mark information, and the AGV subsystem is used to calculate and analyze its location in real time, and then transmitted to the work center computer by wireless communication to manage and plan the overall logistics operation of the industrial site. Progress, avoid mutual interference and improve transportation efficiency.
Vision-based QR code location technology:
Vision-based QR code localization technique: For a two-dimensional code subsystem, the coordinate information of the ground on which the two-dimensional code is directly opposite is stored. The AGV reads and recognizes the two-dimensional code through its own high-resolution telephoto camera, and at the same time, through the rotation of the two-dimensional code image in the camera coordinates, and the electronic compass data, the precise orientation of the AGV can be determined. The information encoded by the two-dimensional code and its position information in the image can be used to completely locate the AGV car.
500kg-1ton load warehouse logistics AGV Parameter:
Weight
|
150kg | 180kg |
Payload
|
500kg
|
1000kg |
Dimension
|
906*710*300mm
|
1100*880*300mm |
Max Speed
|
2m/s
|
1.2m/s |
Guidance Type
|
Visual+2 Dmimensional Code |
|
Obstacle Avoidance
|
Laser Radar
|
|
Communication Mode
|
WiFi·Wifi
|
|
Stop Accuracy
|
<10mm
|
|
Gap
|
<10mm
|
|
Lifting Height
|
≥52mm
|
|
Full Lifting Time
|
≤4s
|
|
Battery Capacity
|
40AH
|
|
Working Hour
|
8 Hours for Full Loaded, It Can Meet Requirements of Continuously Working 24 Hours
|
|
Charge
|
Automatic Charging,Manual Charging,Battery Replacing
|
|
Work Status Light
|
Front / Rear
|
|
Emergency Switch
|
Front / Rear
|
|
Quick Start Button
|
Two Sets Both in Front / Rear
|
|
Charging Method
|
anual Charging or Automatic Charging
|
Logistics agv industry application:
1. E-commerce warehouse sorting:
Nowadays, Internet e-commerce is so prosperous, manufacturers' inventory management and loading capacity directly test the level of their supply chain management, and using the automation technology of storage robots, they can grab and move shelves and goods, and send goods directly to The selection of employees, followed by packaging and delivery, is an effective way to improve the efficiency of warehouse picking, reduce the number of tally personnel, and realize warehouse automation. It can be seen that the development prospects of the application market of warehousing robots and warehousing dispatching and management systems are considerable.
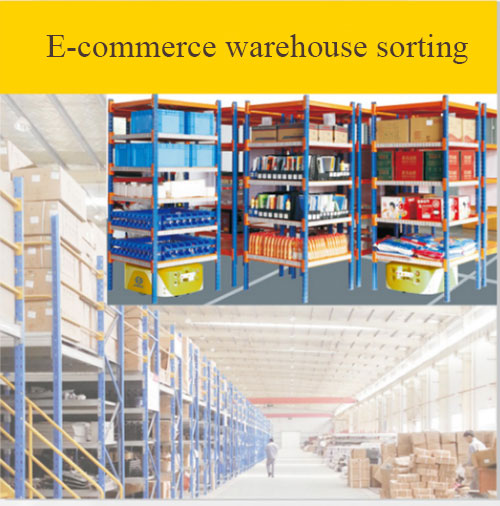
2. Third Party Logistics:
As a third-party automated material handling equipment, AGV can complete battery replacement in one or two minutes, or automatically charge. It can achieve nearly 24 hours of full-load operation, and has the advantage that manual work can't match.
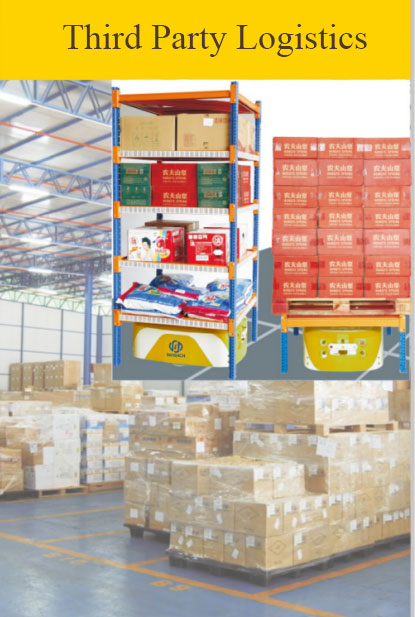
3. Complete sorting logistics in the factory:
In-plant complete sorting AGV, the robot uses inertial two-dimensional code navigation, not only small and flexible, but also high precision and speed; it has the ability to automatically avoid obstacles, freely plan routes, maintain posture and other powerful functions. Logistics agv can move the shelves where the goods are located from the huge warehouse storage area to the employee processing area according to the order, greatly improving the processing efficiency. Using logistics agv can improve storage capacity by nearly 50%.
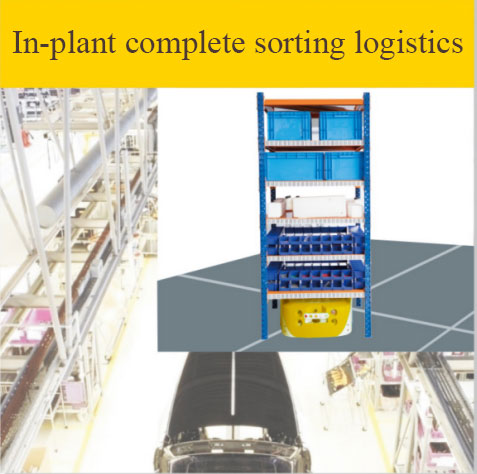
Logistics agv system analysis:
1.System traffic light:
When multiple logistics agv pass the same intersection at the same time, the system adopts the “ traffic light” mode of dispatch;
2. Path re-planning:
In the process of performing tasks, logistics agv can predict that even if the paths conflict, if there is a conflict, the system will adopt the "avoidance" mode and re-plan the subsequent paths;
3.Optimal path planning:
Before the logistics agv performs the task, the system components are scheduled using the "optimal path planning" mode.

The advantages of logistics agv logistics solutions:
1. Reduce labor, replace factory forklifts or oil-electric forklifts, and reduce labor costs;
2. Reduce the labor intensity, reduce the logistics error rate, ensure the product quality, and realize real-time monitoring of the whole process of materials;
3. Improve production efficiency and reduce inventory of turnover products;
4. Improve the level of factory automation, show the strength and image of the company, and enhance the competitiveness of the company.
Danbach Company Information:
Danbach Robot Jiangxi Inc. as a Professional automated guided vehicle manufacture in China. Danbach agv products include forklift AGV,laser AGV,warehouse logistics AGV,lurking AGV,load transfer AGV,lifting AGV, etc.
Danbach has rich experience in the filed of automated device design or application, and offers the worldwide client turn-key solution on remote industrial control device, automated conveyor device, intelligent ASRS system and robot integration.
More about AGVs and other industrial robots please inquiry: info@dbhrobot.com AGV Robots: www.dbhrobot.com